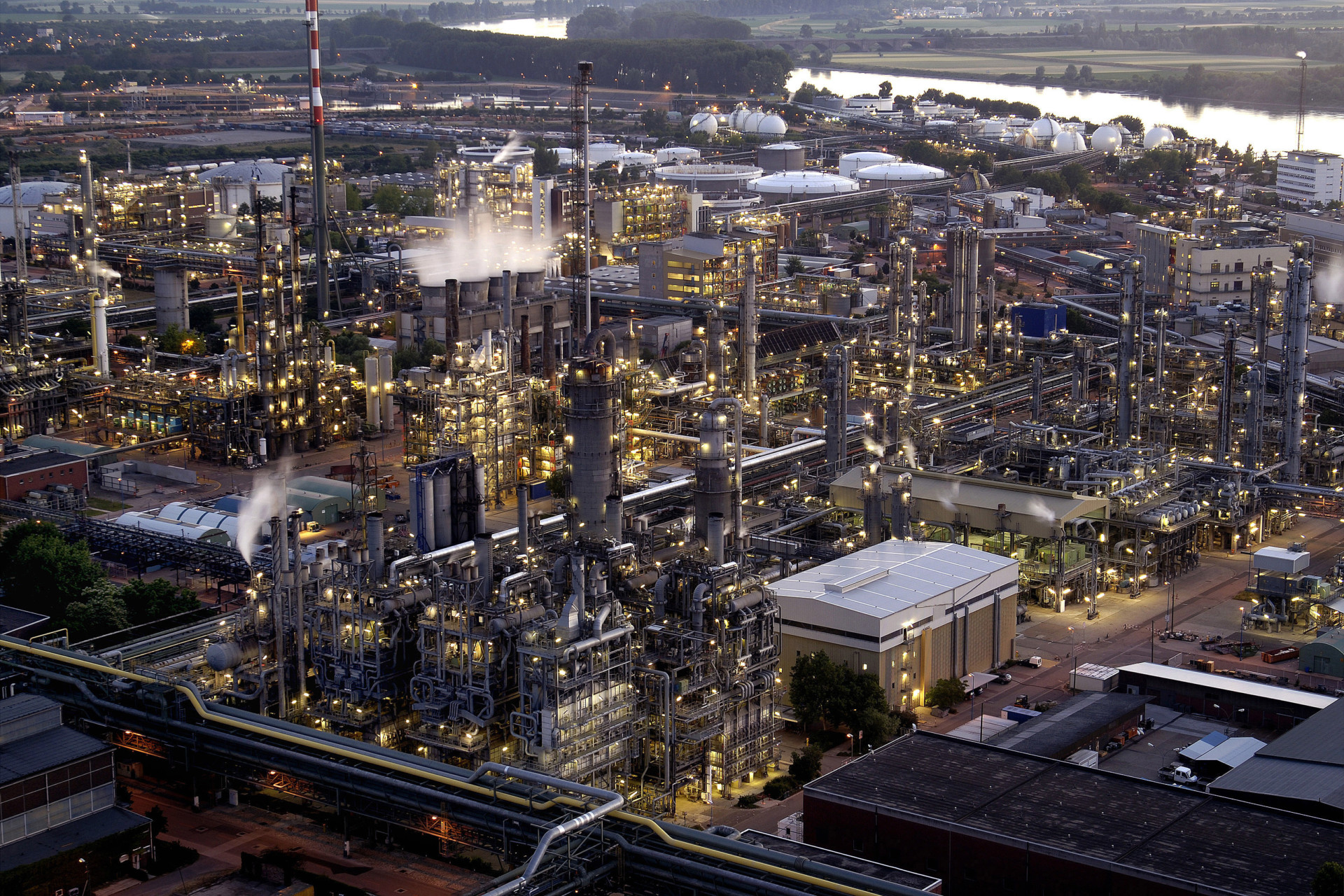
Die BASF SE betreibt an ihrem Verbundstandort in Ludwigshafen Chemiepumpen verschiedenster Bauarten in mittleren fünfstelligen Stückzahlen auf einem Areal von etwa 10 Quadratkilometer. Im Bild zu sehen ist Steamcracker II, die größte einzelne Anlage am Standort Ludwigshafen und Herzstückder Verbundproduktion. Bild: 400_Steam_cracker_at_BASF_Ludwigshafen_site
Herausforderung Pumpen-Instandhaltung: Verschleiß frühzeitig erkennen und Prozessausfälle vermeiden
Pumpen sorgen dafür, dass industrielle Prozesse in verfahrenstechnischen und chemischen Anlagen überhaupt erst zum Laufen oder noch besser in Fluss kommen. Spezialisten im Bereich der Pumpentechnologie mit Exzenterschneckenpumpen und Pumpensystemen, bieten digitale Lösungen zur Überwachung von Pumpen. Zum Beispiel das Unternehmen BestSens und das Fraunhofer IPA haben ihre Lösungen und Wege bei der Instandhaltung von Pumpen. Und BASF hat mit Pumpen verschiedenster Bauarten in mittleren fünfstelligen Stückzahlen auf einem Areal von 10 km² verteilt jede Menge Erfahrung auf diesem Gebiet.
Mit Monitoring-Systemen erkennen Unternehmen Verschleiß frühzeitig und vermeiden Prozessausfälle vor ihrer Entstehung. Die Datenerhebung erfolgt meist automatisch an der Pumpe, Analysen können in den Cloud Connected Services vorgenommen werden, doch die Aufgabenstellung ist nicht immer einfach, dazu Wolfgang Diller, CTO der BestSens AG, einem Anbieter von High-Tech Sensorik: „Pumpen in verfahrenstechnischen und chemischen Anlagen instand zu halten, birgt verschiedene Herausforderungen. Verschleiß und Korrosion sind wichtige Probleme, da Pumpen häufig aggressiven Substanzen ausgesetzt sind. Regelmäßige Inspektionen und Wartungsmaßnahmen sind entscheidend, um den Zustand der Pumpenkomponenten zu überwachen und vorzeitigen Ausfällen vorzubeugen.“
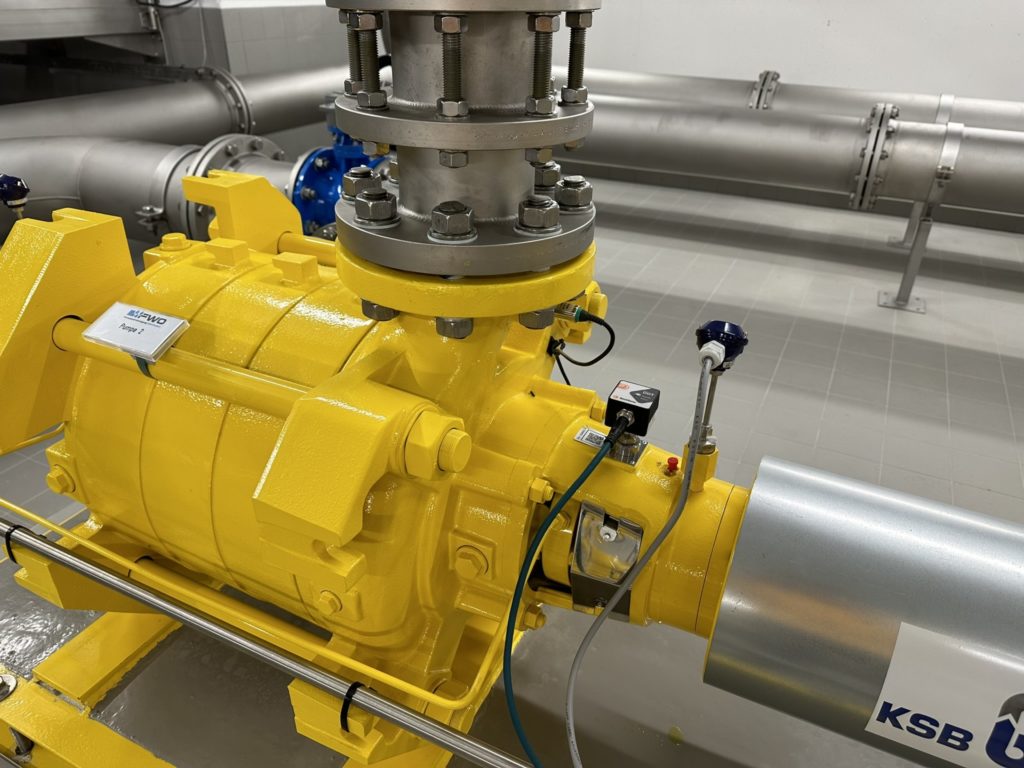
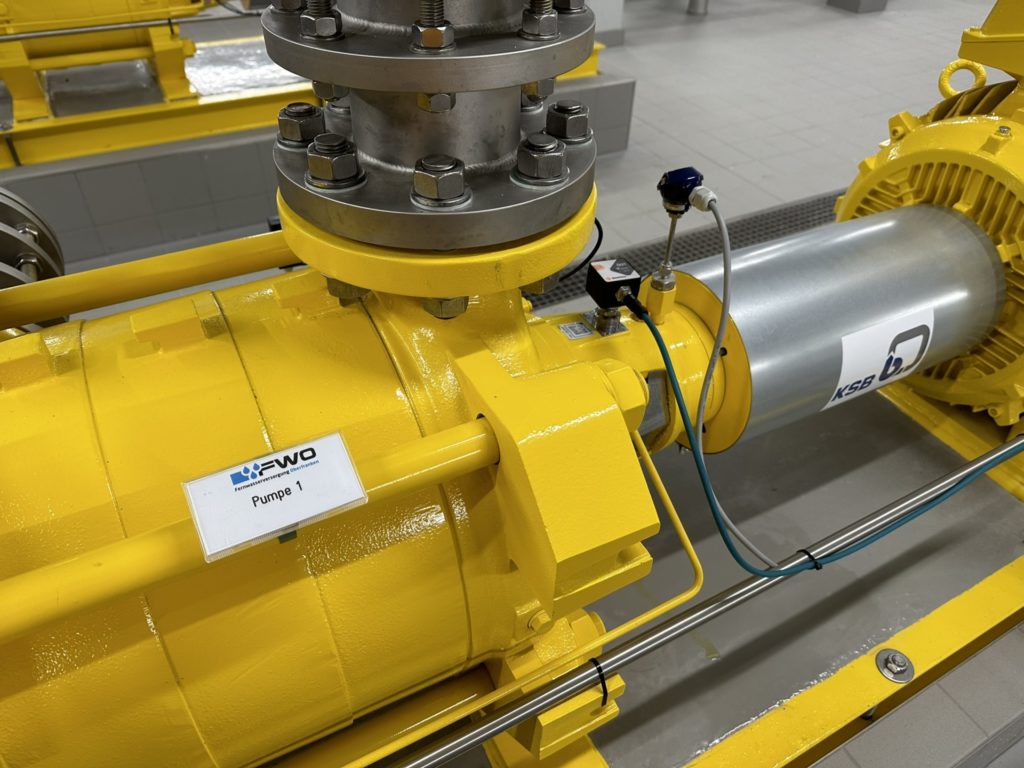
Smarte Pumpenüberwachung mit vibDOT: Die Messwerte zu Temperatur und Vibration werden direkt am Gehäuse der Pumpe erfasst und über ein Ethernet an die DOTbox übertragen, von dort via LTE in die Cloud. Die Benutzeroberfläche ermöglicht die sofortige Einsicht in den Verlauf und aktuelle Daten. Bilder: BestSens vibDOT bei FWO_1 und BestSens vibDOT bei FWO_2
BASF: Pumpen in 200 Produktionsanlagen verteilt
Die BASF SE etwa betreibt allein an ihrem Verbundstandort in Ludwigshafen Chemiepumpen verschiedenster Bauarten in mittleren fünfstelligen Stückzahlen auf einem Areal von 10 km². „Die Pumpen sollten ebenerdig mit entsprechender Zugangsfläche (mindestens Palettenbreite) installiert werden“, sagt Jürgen Weinerth, Senior Expert Process Pump Technology, Global Engineering Services BASF. „Über großen und schweren Pumpen sollten Stahlträger zum Anschlag von Hebezeugen vorgesehen werden. Aufgrund von Platzproblemen oder komplexen Rohrleitungsführungen ist der Aus- und Einbau in der Praxis jedoch oft sehr zeitintensiv.“ Bei BASF sind die Pumpen über die gesamte Werksfläche des Verbundstandortes in etwa 200 Produktionsanlagen verstreut. Die Transportlogistik ist eine Herausforderung, seit einiger Zeit unterstützt das sogenannte Equipment-Tracking bei der Verfolgung der Pumpen.
Lange Wegstrecken und -zeiten und begrenzte Zugänglichkeit
Auch Dipl.-Ing. Thomas Adolf, Leiter der Gruppe Instandhaltungsmanagement am Fraunhofer-Institut für Produktionstechnik und Automatisierung IPA, sieht noch ganz andere Herausforderungen: „Wir haben zunächst einmal in Prozessanlagen oder Chemie-Industrieparks oft über Jahrzehnte gewachsene Strukturen, was die Versorgungspumpen angeht. Daraus resultiert, dass es keinerlei Standardisierung bei den Pumpen gibt und eine sehr hohe Variantenvielfalt. Aufgrund des Alters und der Vielfalt haben wir zudem teilweise Lücken in der technischen Dokumentation und daraus abgeleitet natürlich auch Probleme bei der Integration einer neuen Pumpe. Und wenn es keine aktuelle Dokumentation gibt oder diese nicht zur Verfügung steht, ist es schwierig zu identifizieren, welcher Pumpentyp exakt gerade ausgefallen ist.“ Dazu kommt, dass bei diesen Anlagen immer lange Wegstrecken und -zeiten und oft auch eine begrenzte Zugänglichkeit zu berücksichtigen sind, weil die betroffene Pumpe vielleicht in einem Keller untergebracht ist, der verschlossen ist. Die Branchen Prozessindustrie und Chemie haben in den vergangenen Jahren zudem Redundanzen abgebaut. Wo also vor einigen Jahren noch zwei identische Pumpen verbaut waren und wechselnd zum Einsatz kamen, finden wir heute oft nur noch eine vor.
IPA-Mann Adolf dazu: „Was in der Prozessindustrie noch dazu kommt, sind die transportierten Stoffe, die eine Gesundheits- oder Umweltgefährdung darstellen können. Chlorgas zum Beispiel, oder abrasive Stoffe, die auf Materialien, Dichtungen etwa, massiven Einfluss haben. Und was bei Pumpen, die überall auf dem Gelände verteilt sind, eben auch fehlt, ist die Inspektion im Vorbeigehen. Wer durch eine Produktionshalle geht, nimmt unwillkürlich visuelle oder akustische Reize wahr, merkt also, wenn etwas nicht stimmt. An verteilten Anlagen, an denen niemand vorbeikommt, bemerkt man Undichtigkeiten oder Störgeräusche natürlich nicht.“
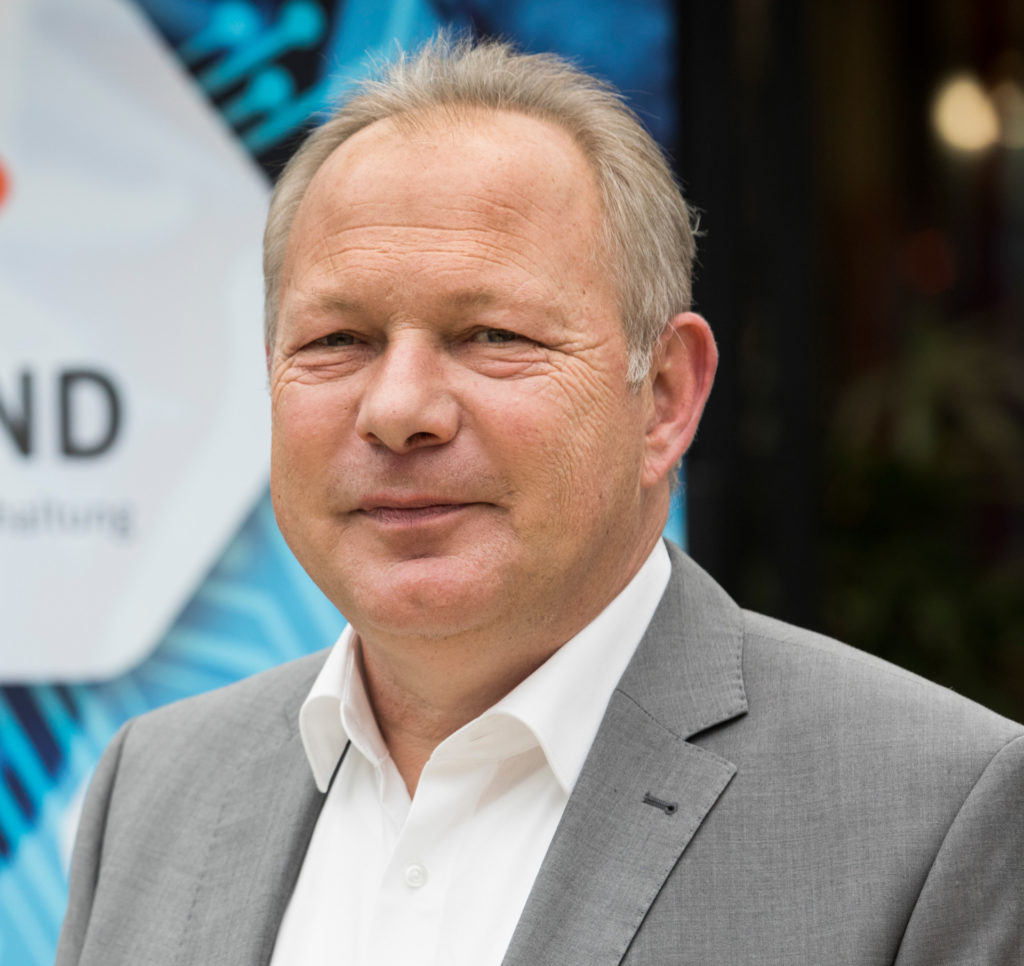
Thomas Adolf, IPA: „Für uns ist das gesamte Wertschöpfungssystem in der Prozessindustrie interessant, also die Produktherstellung und da ist eine einzelne Pumpe natürlich nur ein Element. Wenn wir aber eine kritische Pumpe ausgemacht haben, optimieren wir die Instandhaltungsstrategie für diese Pumpe und führen bei Bedarf ein digitales Retrofit durch.“ Bild: Portrait_Thomas_Adolf
„Pumpentausch sollte in zwei Stunden möglich sein“
Bei BASF am Standort in Ludwigshafen werden noch ältere Pumpen betrieben, die bei den Herstellern inzwischen aus dem Programm genommen wurden oder bei denen der OEM gar nicht mehr existiert. Ersatzteile können nur schwer oder gar nicht mehr beschafft werden. Als alternative Beschaffungswege spielen Reverse Engineering und die Möglichkeit der additiven Fertigung eine immer wichtigere Rolle. „Um eine schnelle Verfügbarkeit von Pumpen bei Ausfall zu gewährleisten, werden bestimmte Pumpentypen und Baugrößen einem zentralen Versorgungszentrum (Pumpenpool) für die Betriebe bevorratet“ so BASF-Mann Jürgen Weinerth. „Ein Pumpentausch sollte in zwei Stunden möglich sein. Die Bevorratung von Pumpen ist aber betriebswirtschaftlich nur sinnvoll, wenn diese in einer gewissen Stückzahl in mehreren Anlagen am Standort eingesetzt werden.“
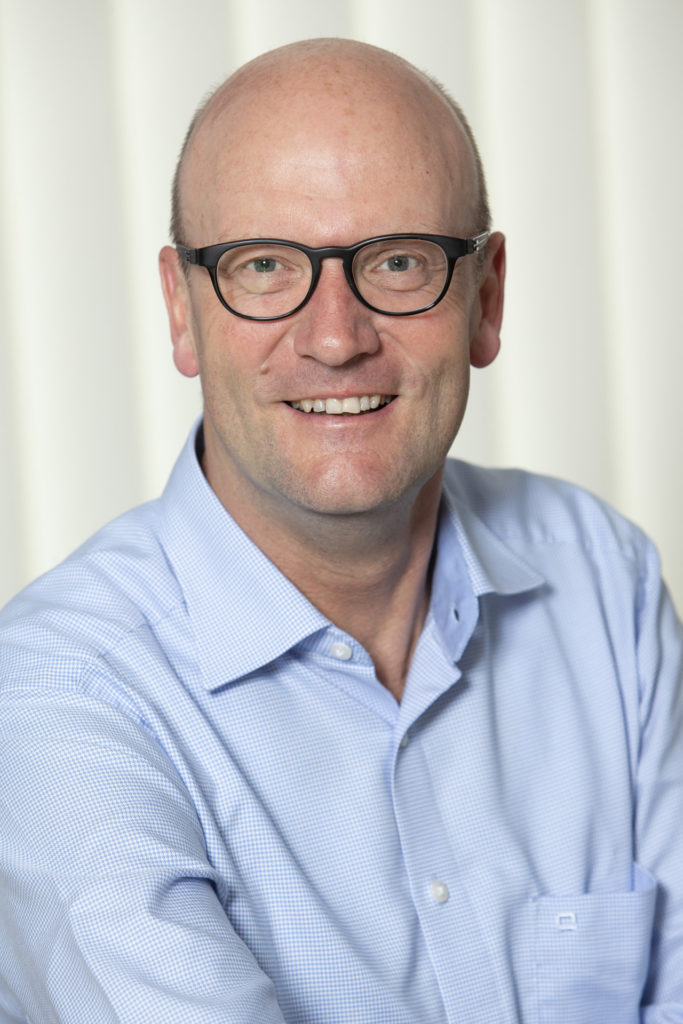
Jürgen Weinerth, BASF: „Eine weitere Herausforderung der Instandhaltung sind Reparaturen der meist chemisch kontaminierten Pumpen. Die Pumpen müssen vor dem Ausbau in der Anlage gespült werden. Die Reparatur der Pumpen erfolgt in einer zentralen Fachwerkstatt.“ Bild: S180061_Weinerth
„Fachkräftemangel ein erhebliches Problem“
Entscheidend ist die Minimierung von Ausfallzeiten. Diese erfordert effektive Instandhaltungsstrategien, präventive Maßnahmen und geplante Stillstände, um einen reibungslosen Anlagenbetrieb zu gewährleisten. Daher ist der Einsatz fortschrittlicher Überwachungssysteme, einschließlich Zustandsüberwachung und Diagnose, für die Früherkennung von Problemen unerlässlich. Eine vorausschauende Instandhaltung kann unerwartete Ausfälle verhindern, Wolfgang Diller ergänzt: „Doch auch hier ist der Fachkräftemangel ein erhebliches Problem. Es gibt immer weniger Personal, das sich um immer mehr Ausrüstung kümmert. Das bedeutet, dass Mitarbeiter weniger Zeit pro Anlagenteil haben oder die Zeitabstände zwischen den Rundgängen immer größer werden. Die Priorisierung von Wartungsarbeiten ist entscheidend.“ Der Einsatz von Messtechnik kann dabei helfen. Sie verschafft einen kontinuierlichen Gesamtüberblick und Mitarbeiter können sich dann auf Bereiche konzentrieren, in denen Auffälligkeiten durch die Sensorik detektiert werden. Darüber hinaus sind die Betriebsstunden bekannt, sodass Wartungsarbeiten auch nach Laufleistung eingetaktet werden können. „Wir stellen diese Messtechnik zur Verfügung, um möglichst kostengünstig und mit geringem Personalaufwand Anlagen zu überwachen. Die Instandhaltung realisiert das Personal vor Ort, also die Anlagenhersteller oder Servicefirmen mit entsprechenden Werkstätten“, so Diller weiter.
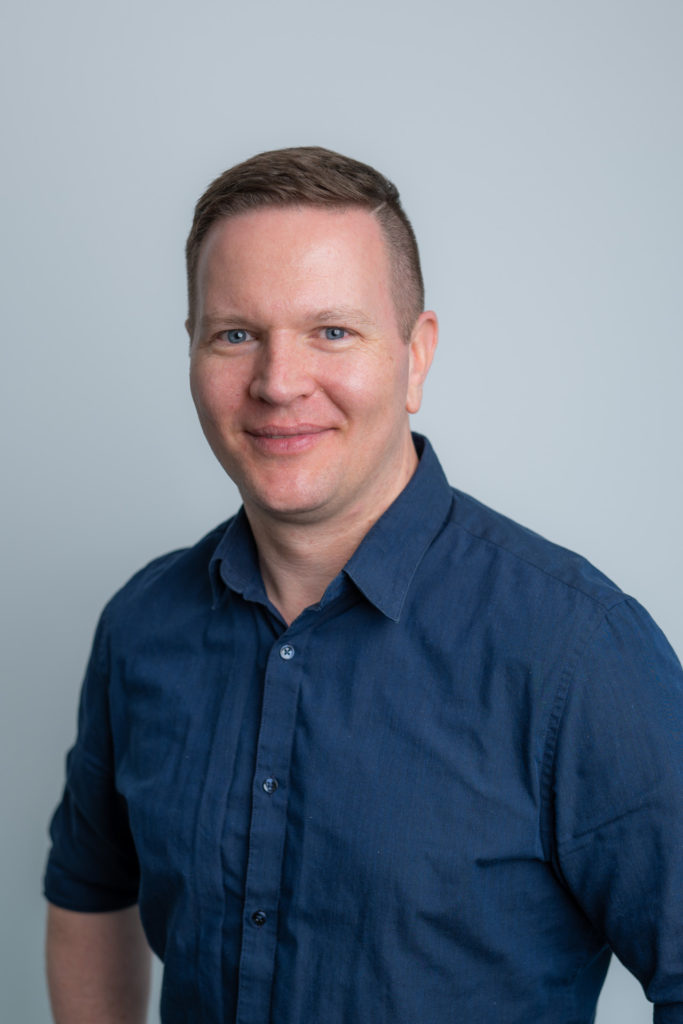
Wolfgang Diller, BestSens: „Regelmäßige Inspektionen und Wartungsmaßnahmen sind entscheidend, um den Zustand der Pumpenkomponenten zu überwachen und vorzeitigen Ausfällen vorzubeugen.“ Bild: Mitarbeiterportrait_300dpi_21 Diller
„Roboter können bei Inspektion von Anlagen unterstützen“
Bei BASF etwa steuern in SAP hinterlegte Wartungspläne die jeweiligen Instandhaltungsaufgaben. Diese können Sichtkontrollen, Nachschmierung der Wälzlager oder auch händische Schwingungsmessungen beinhalten. Power Apps und Tabletts unterstützen inzwischen bei Wartungsrundgängen. Aufgaben wie das Abarbeiten von Checklisten können direkt auf dem Tablett durchgeführt und dokumentiert werden.
„Zukünftig könnten Roboter Routineaufgaben bei der Inspektion von Anlagen unterstützen. Verschiedene technische Lösungen sind momentan in der Erprobung“, erläutert Jürgen Weinerth. „Die AIRA Challenge (Advanced Industrial Robotic Applications) – ein internationaler Wettbewerb zur Automatisierung von Service- und Inspektionsaufgaben in chemischen Produktionsanlagen durch den Einsatz von Robotertechnologie – zeigte interessante Einsatzmöglichkeiten von Robotern.“
Auch das Fraunhofer IPA bietet mit MIMROex einen Prototyp eines Off-shore-Inspektionsroboters an. Auf Offshore-Plattformen sowie in chemischen und petrochemischen Produktionsanlagen mit einem hohen Automatisierungspotenzial kann MIMOROex Überwachung aktueller Pegelstände und Anzeigen von Messgeräten ermöglichen. Dazu zählen die akustische Inspektion etwas von Pumpen, die Untersuchung auf Leckage, die Entnahme von Proben sowie die Wartung stationärer Feuer- und Gassensoren.
Pumpwerk setzt auf Condition-Monitoring mit vibDOT
BestSens bietet mit vibDOT eine Lösung für effizientes Condition-Monitoring und sensorbasierte Überwachung von rotierenden Anlagen an. vibDOT kann Schwingungen, Temperatur und Drehzahl überwachen. Dies ermöglicht auch eine Aussage über die Drehrichtung und bietet eine Start-Stop-Erkennung. Ergänzt wird dieses System durch sealDOT. Diese Lösung kann zusätzlich zu den genannten Parametern auch die Gleitringdichtung überwachen. Durch die kompakte Größe kann dieser auch kleine Pumpen problemlos überwachen. So kommt etwa seit Oktober 2023 der kompakte Multisensorknoten vibDOT im Pumpwerk der Fernwasserversorgung Oberfranken (FWO) am Rötelsberg im Landkreis Bamberg zum Einsatz. Der frisch eingeweihte Hochbehälter mit Pumpwerk – Teil des sogenannten Scheßlitzer Astes von Bamberg bis Mainleus – dient der Sicherstellung der
Trinkwasserversorgung für die Bevölkerung. Seit seiner Inbetriebnahme im Oktober 2023 unterstützt der vibDOT die hochmoderne Anlage durch die Erfassung von Vibration und Temperatur der Pumpen vor Ort während des Betriebs. Die integrierten Sensoren senden die Daten direkt in die Cloud. „Die Fähigkeit des vibDOT, Echtzeitdaten zu sammeln und Warnmeldungen bereitzustellen, spielt eine entscheidende Rolle bei der frühzeitigen Erkennung von Abweichungen und potenziellen Problemen. In der Wasserversorgung ist diese Proaktivität von essenzieller Bedeutung für die Minimierung von Ausfallzeiten und die Sicherstellung einer kontinuierlichen Versorgung“, so Wolfgang Diller.
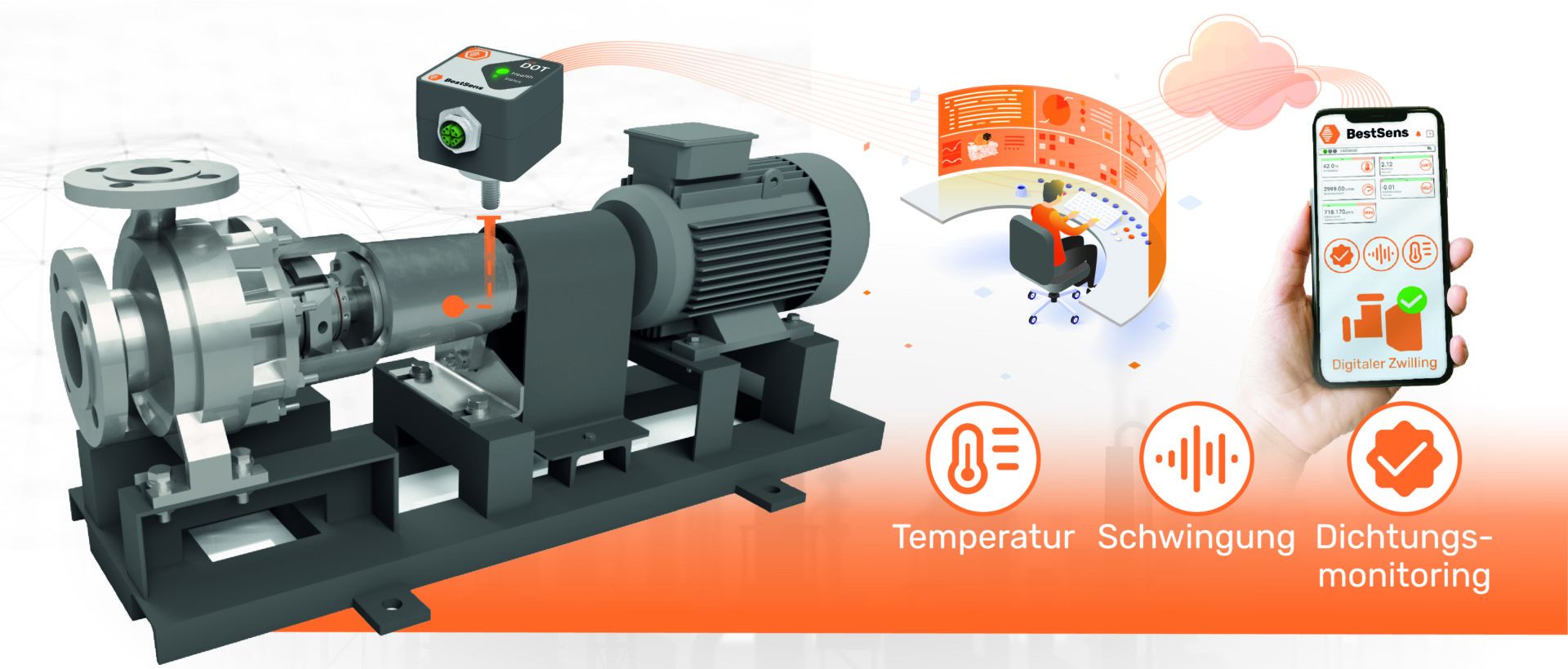
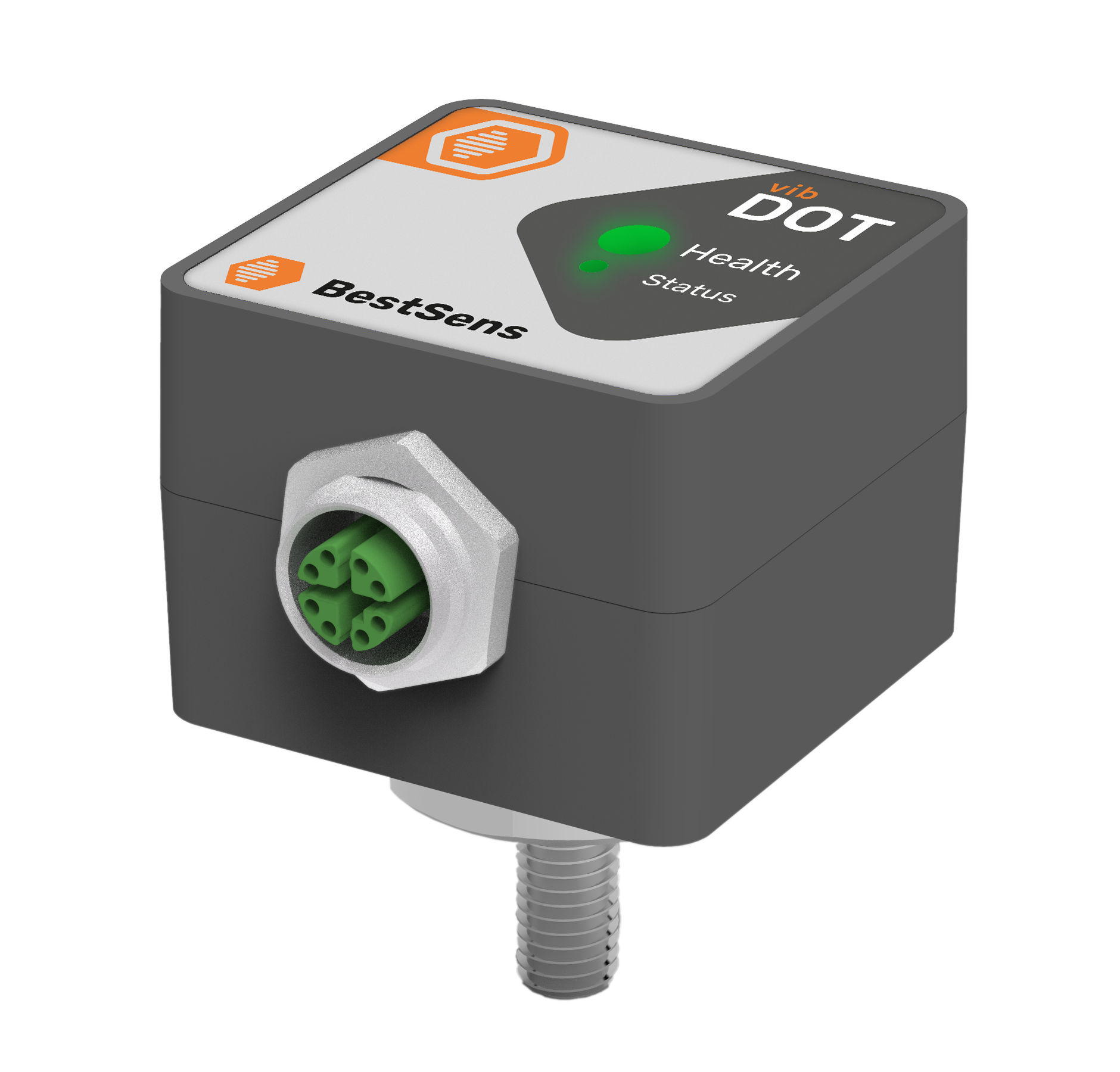
Die Fähigkeit von vibDOT, Echtzeitdaten zu sammeln und Warnmeldungen bereitzustellen, spielt eine entscheidende Rolle bei der frühzeitigen Erkennung von Abweichungen und potenziellen Problemen. Durch die kompakte Größe kann vibDOT auch kleine Pumpen problemlos überwachen. Bilder: 2023_10_23_DOT Plattform und 2023-07_26_DOT NEU_freigestellt
Konsequenzen für das Wertschöpfungssystem bei Ausfall entscheidend
Um geeignete Instandhaltungsstrategien festzulegen, werden beim Fraunhofer IPA zunächst die einzelnen Elemente (Maschinen und Equipments) des Wertschöpfungssystems im Rahmen eines Risk Assessments proirisiert. Ein wesentlicher Faktor sind hierbei die Konsequenzen für das Wertschöpfungssystem beim Ausfall der einzelnen Elemente. „Wir nutzen eine Checkliste, teilweise auch ein Simulationstool, um herauszufinden, wie wichtig einzelne Elemente, also auch Pumpen, im gesamten Wertschöpfungssystem sind und je nach Wichtigkeit, leiten wir verschiedene Instandhaltungsstrategien daraus ab“ sagt Adolf, Leiter der Gruppe Instandhaltungsmanagement beim IPA. Neben der Anpassung der Wartungspläne, der Bevorratungsstrategie für Ersatzteile oder organisatorischen Maßnahmen, werden im Rahmen eines Risk Managements auch Empfehlungen zur Überwachung von kritischen Komponenten abgeleitet. „Wir richten also ein Condition Monitoring ein, überlegen welche Daten erfasst und ausgewertet werden müssen, welche Sensoren dafür nötig und welche Überwachungsstrategien geeignet sind. Im nächsten Schritt werden Verscheißmodelle entwickelt, Alarmgrenzen definiert und falls möglich Restlebensdauerberechnungen abgeleitet“ so Adolf weiter.
„Gesicherte Übertagung der Daten und Abgriff durch Dritte verhindern“
Je nach Kritikalität der Pumpen kommen bei ABASF verschiedene Überwachungssysteme zum Einsatz. Hochkritische Maschinen werden mit kabelgebundener Sensorik permanent online überwacht. Neben der Instrumentierung mit verschiedener Sensorik ist die Einbindung der Prozessdaten aus dem Prozessleitsystem in die Überwachung notwendig, um eine Interpretation unterschiedlicher Betriebspunkte zu ermöglichen. Für diese Art der Überwachung betreibt die BASF ein sog. Reliability Center. Kritische Standardpumpen werden mit kabellosen Schwingungssensoren überwacht, da die Sensoren nur zur Überwachung verwendet werden und keine Regel- oder Schaltfunktionen erfüllen müssen. Diese Sensoren werden batteriebetrieben und übertragen die Messdaten mittels einer kabellosen Kommunikationstechnologie. Die Übertragung der Messdaten kann mithilfe unterschiedlicher Kommunikationstechnologien erfolgen. Diese sind WiFi, LoRaWAN, WirelessHART, Wirepas Mesh und weitere. „Wichtig ist“, so Pumpenexperte Jürgen Weinerth, „dass die verwendete Technologie eine gesicherte Übertagung der Daten ermöglicht und ein Abgriff der Daten durch Dritte nicht möglich ist. Die kontinuierliche Überwachung erlaubt eine Aussage über den aktuellen Betriebszustand und eine Bewertung vorhandener oder sich anbahnender Schäden. Sie stellt somit die Grundlage einer zustandsorientierten vorhersagenden Instandhaltung (Predictive Maintenance) dar.“