Pandemie und Lockdown treiben in vielen Branchen die Digitalisierung voran. Auch in der Instandhaltung dürfte der Zeitpunkt gekommen sein, alte Vorurteile über Bord zu
werfen. Eine Bestandsaufnahme.
So hebt Corona die Instandhaltung auf ein neues Level
Für manchen Instandhalter mag der zeitweise Corona-bedingte Lockdown auch seine Vorteile gehabt haben. Viele Unternehmen ließen Überstunden abbauen oder gingen in Kurzarbeit, womit sie ihre ruhenden Produktionsanlagen in Ruhe warten und auf den neuesten Stand bringen konnten. Das gilt vor allem für solche Firmen, in denen noch keine modernen Condition-Monitoring-Systeme im Einsatz sind – für die ist ein längerer Anlagenstillstand oftmals hilfreich.
Nun wird sicher niemand behaupten, dass eine Situation wie im Frühjahr 2020 wünschenswert wäre. Das technische Servicepersonal wird während einer Krise auf eine harte Probe gestellt. Denn auch während einer Pandemie ist es wichtig, ungeplante Störungen in der Produktion zu vermeiden, nicht nur bei wichtigen Produkten wie Atemschutz-Masken oder Medikamenten. Monteure und Techniker stehen oft an vorderster Front, wenn es darum geht, den Betrieb von Maschinenparks am Laufen zu halten, und das nicht nur bei kritischen Infrastrukturen wie in der Energieversorgung und bei Netzbetreibern. Entsprechend stellt sich die Frage, was die Instandhaltungsbranche aus dem Covid-Lockdown lernen kann.
Denn so, wie die Büro-Kollegen gelernt haben, auf Dienstreisen und persönliche Meetings zu verzichten, schlicht weil sie mussten, so machen auch Instandhalter die Erfahrung, dass zum Beispiel Service-Techniker nicht anreisen dürfen. Und so, wie noch vor kurzem in vielen Büros Home-Office undenkbar war, so war es in vielen Anlagen undenkbar, dass sich externe Dienstleister remote auf die Maschinen aufschalten dürfen. Corona zeigt sich hier wie da als Digitalisierungsbeschleuniger. Wie gut, dass Technologien wie Smartphones, Cloud-Services und Augmented Reality bereits erfunden sind!
Smarte Instandhaltung hilft allen
In erster Linie haben Instandhalter für die dauerhafte Verfügbarkeit der Anlagen zu sorgen. Doch das ist nicht alles: In Zeiten von Industrie 4.0 mit seiner steigenden Flexibilität der Produktion – kleine Stückzahlen, hohe Produktvarianz – zeigt sich, dass die meisten Veränderungen der Produktionsanlagen zusammen mit den Technikern von der betrieblichen Instandhaltung umgesetzt werden.
In der Corona-Krise zeigte sich dieser Effekt sogar verstärkt: Egal, ob Unternehmen ihre Produktion umstellen mussten, weil Lieferketten ausfielen oder weil kurzfristig andere Produkte (Desinfektionsmittel statt Schnaps…) gefertigt werden sollten: Die Rolle einer intelligenten Instandhaltung ist nicht zu unterschätzen.
Möglichkeiten gibt es viele. Digitale Lösungen zur Einsatzplanung und mobilen Auftragsabwicklung helfen dabei, Aufträge zuverlässig zu planen und vor Ort auszuführen. Moderne Field-Service-Management-Systeme ersetzen bestehende, papierbasierte Prozesse. Und die Zentrale weiß immer, wer wann wohin muss. Das ist allerdings nur zu schaffen, wenn die Basis gelegt ist. Condition Monitoring, eines der ursprünglichsten Ziele von Industrie 4.0, ermöglicht nicht nur die zustandsbasierte Wartung einer Maschine.
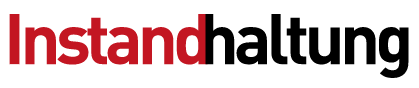